Custom Features for Rack Mount System Enclosures
Electronic Enclosures, Inc. (EEi) has decades of expertise in design, fabrication, thermal dissipation, and EMI/RFI containment. Our focus here is on the design and production of custom rack mount chassis for almost any industry. Our first involvement with RAID systems goes back to Micropolis and full-height 5¼ drives; copper or fiber switches to any number of ports to maximum chassis density; photonics applications up to PAM4; servers, long & short depth, blades to 4U; audio/video recording, editing and streaming. Many systems are considered – must not fail – “performance or mission critical” with redundant hot-swap power and fans, redundant or N+1 electronics modules, and card cages.
Our primary customers establish the performance requirements and produce the electronics, software/firmware, and test requirements. EEi jointly collaborates on engineering and manufacturing the chassis with power & cooling, resulting in the production of rack mount system enclosures.
1U Custom Rack Mount Enclosure with 48 SFP+ Ports & Console
24 NVMe drives for Multi-Petabytes of RAID Data Storage in a 2U Custom Rack Mount Chassis
Custom SCADA Firewall 1U Rack Mount Chassis
5U Custom Card Cage & Backplane and Convection Fan Cooling
Designing for Mission Critical Field Maintenance
This Joint collaboration at the onset of system development enormously benefits thermal dissipation results. In critical applications, hot-swap fan redundancy is used. EEi designs and manufactures custom hot-swap fan assemblies.
We frequently design and build in hot-swap power supplies. These may be custom or COTS modules. CRPS supplies are used most frequently. We design, produce, and install a power distribution board, which often includes additional rails.
Field replaceable electronics or FRUs make for easy field upgradability and can be designed for nearly any size or configuration. They may plug into an interposer board or directly into a main board and are typically blind-mate and hot-pluggable.
Improved Accuracy and Flexibility in Production Card Cages
Card cages can be designed into rack mount enclosures with plug-in cards in either a horizontal or vertical orientation with a horizontal or vertical backplane or center-plane. Airflow is either horizontal or vertical based on the plug-in card orientation. Most bus structures can be accommodated: VME, VPX, VXS, cPCI, ATCA, or fully custom etc.
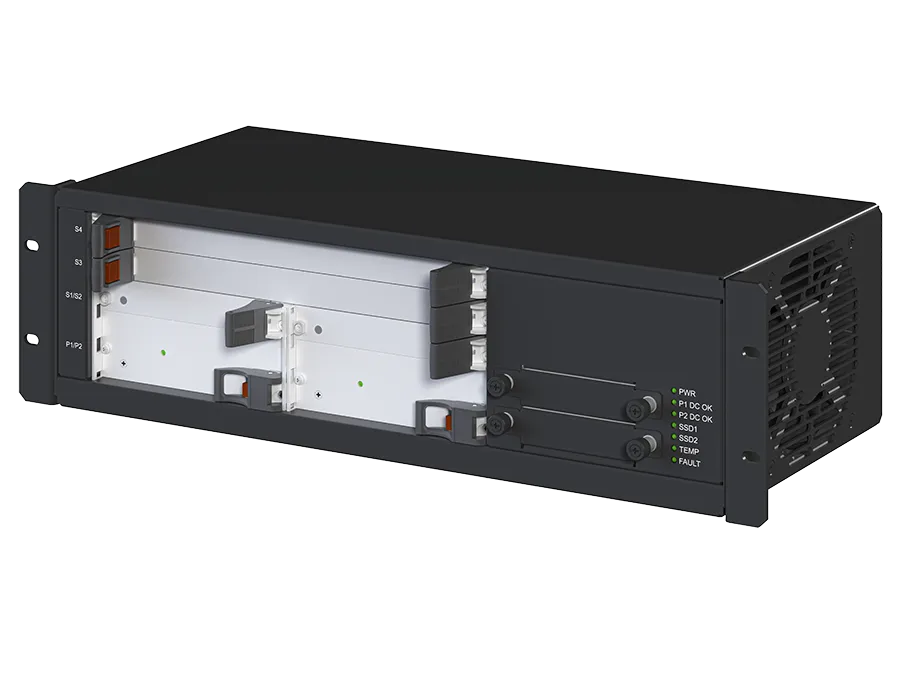
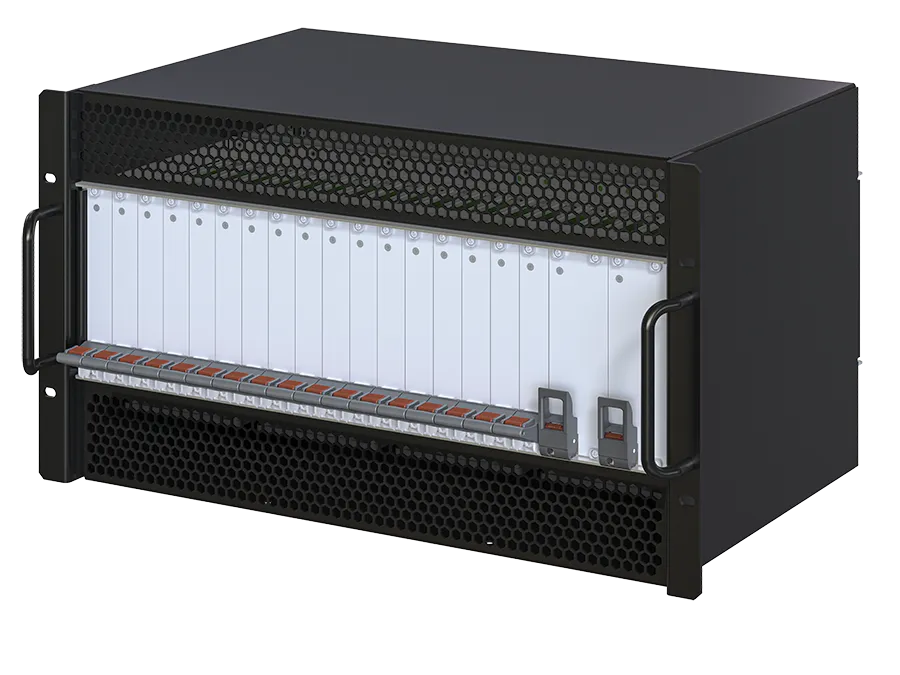
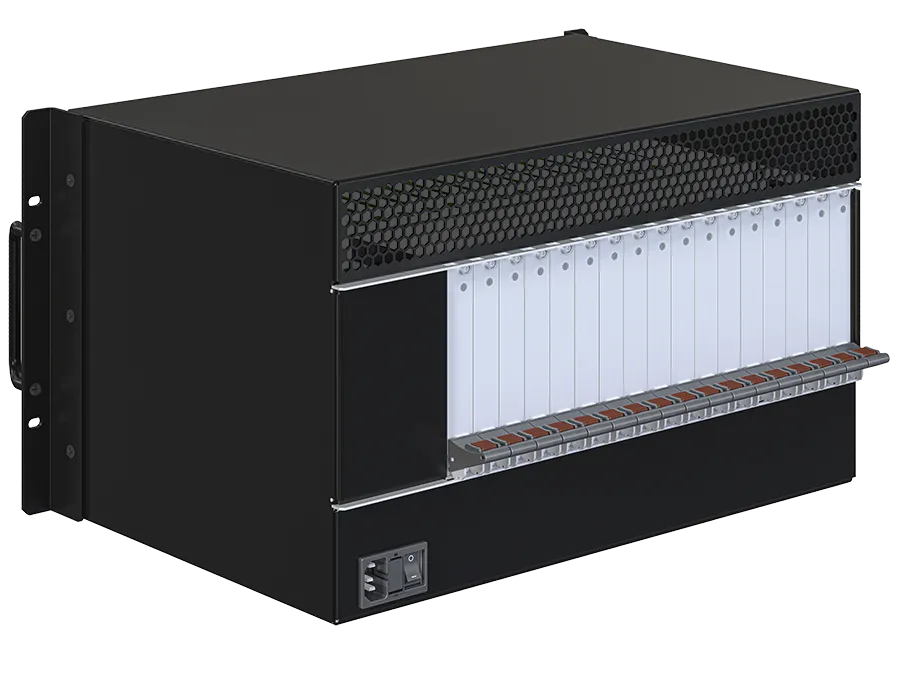
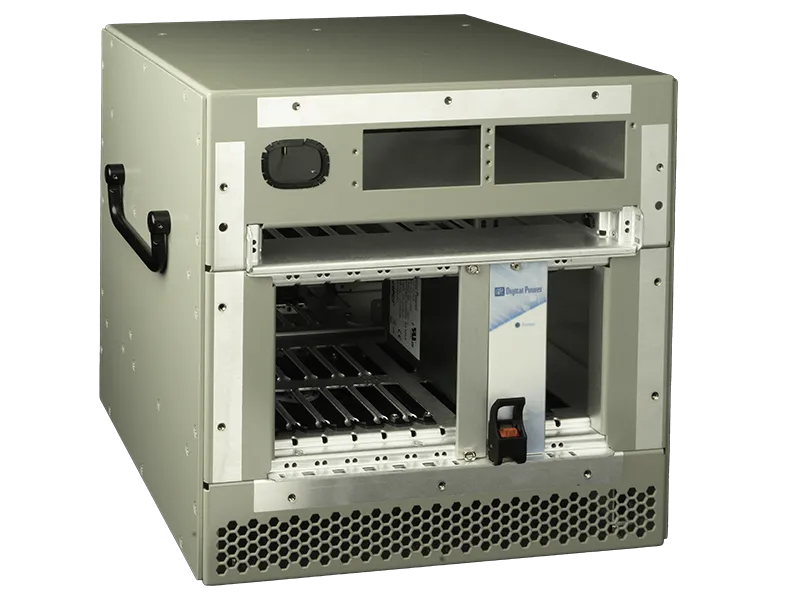
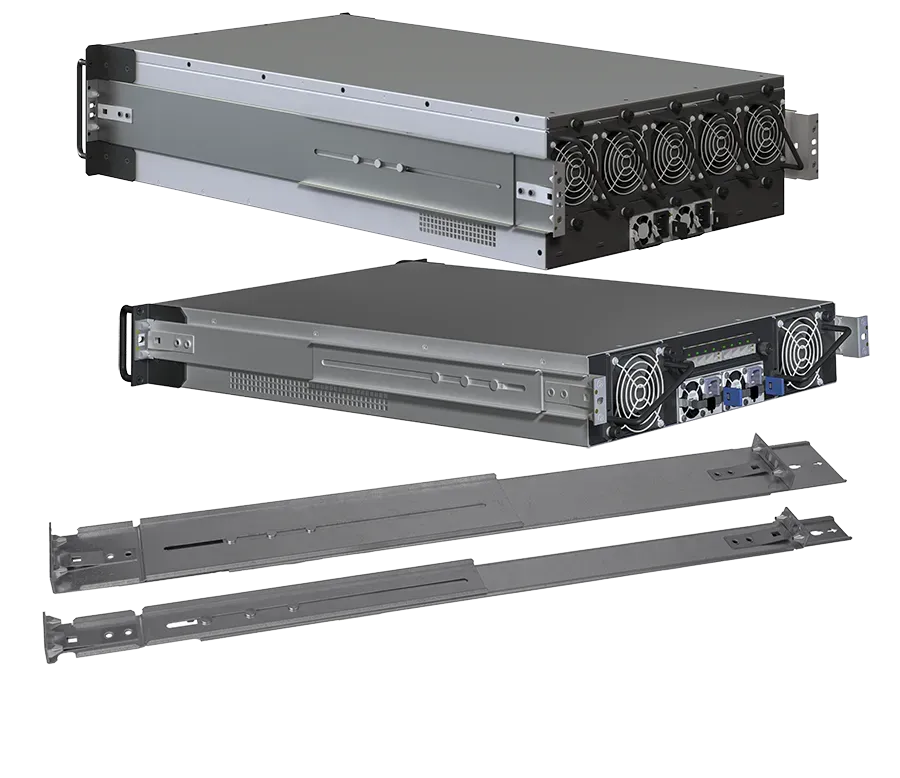
Tool-less Rack Mount Chassis Slide Rails
Rack mount chassis slide rails used with deeper enclosures typically require hardware and tools to install the system chassis into the rack. EEi has developed a rack mount chassis slide rail that requires neither, aka, a tool-less slide rail. These rails are designed to “click” onto the side of its associated rack mount enclosure as well as “click” into the racks’ RETMA rails with the square hole pattern. It is fast and simple and just as easy to remove.