Custom Rack Mount Card Cages
EEi Designs and Manufacturers Custom Card Cages Systems with Forced Air Cooling for Production Applications.
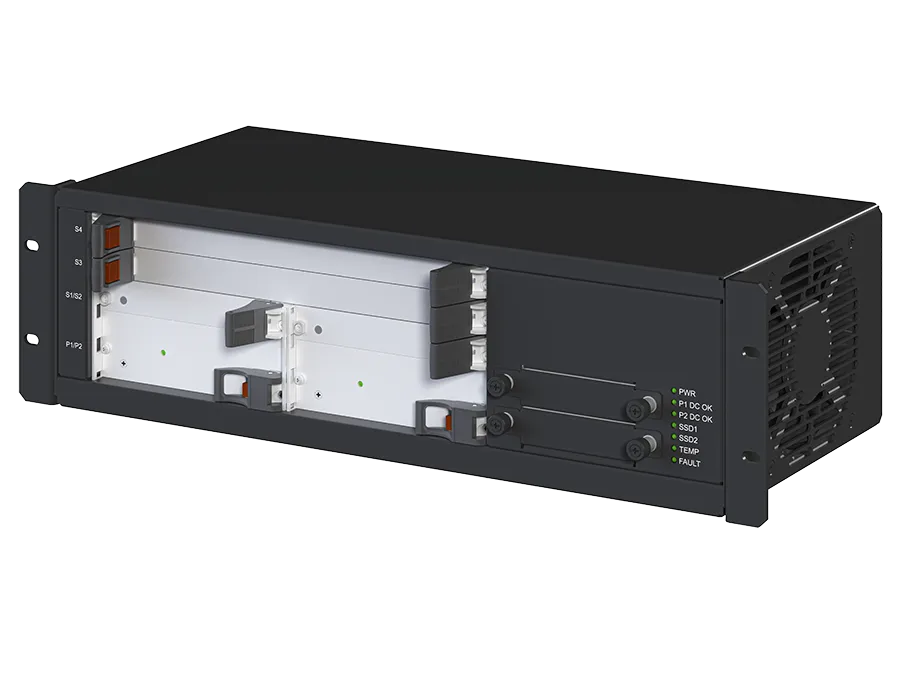
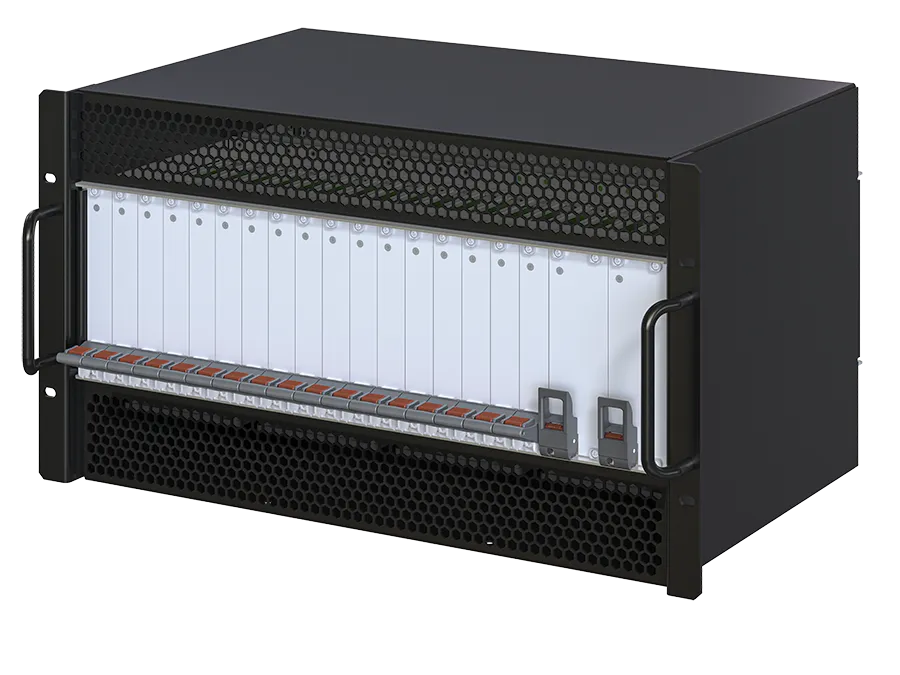
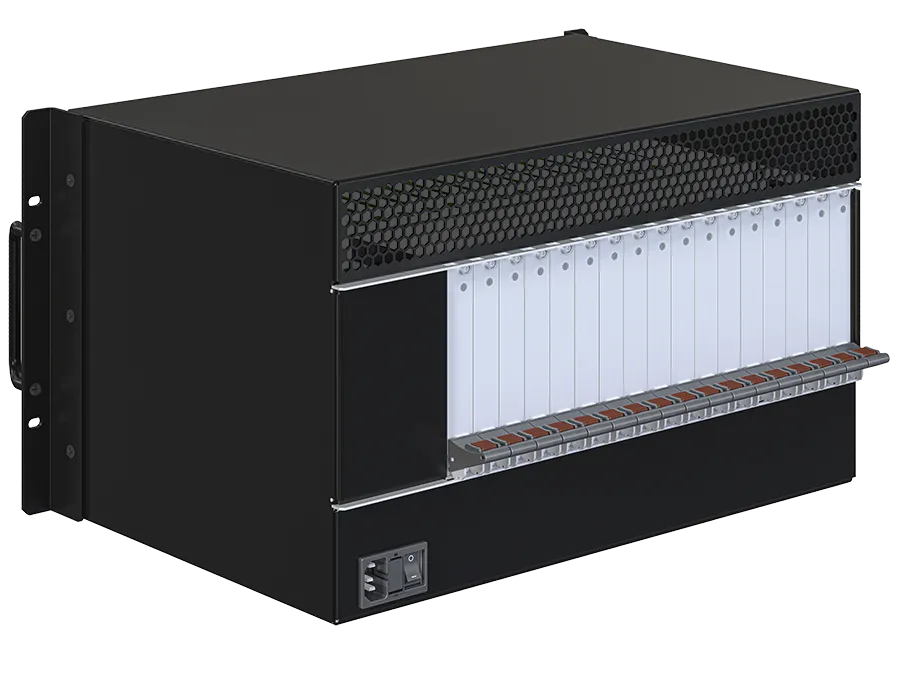
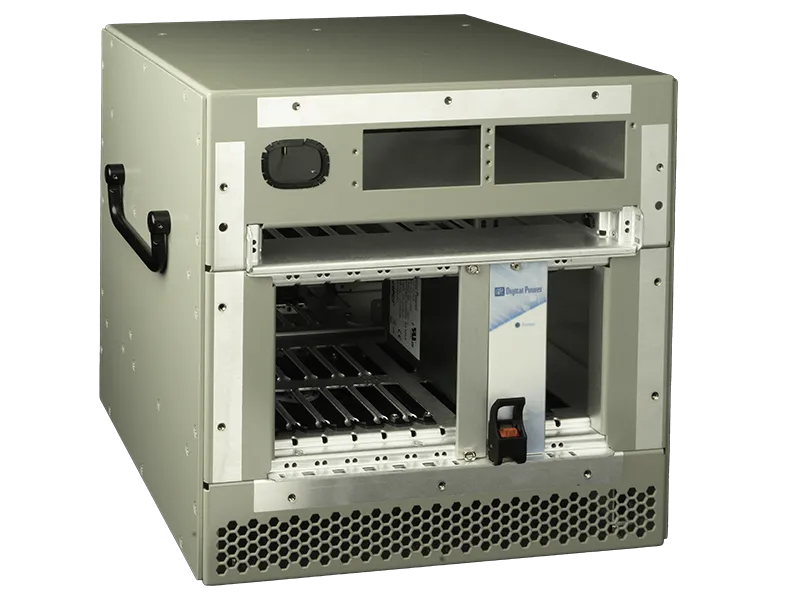
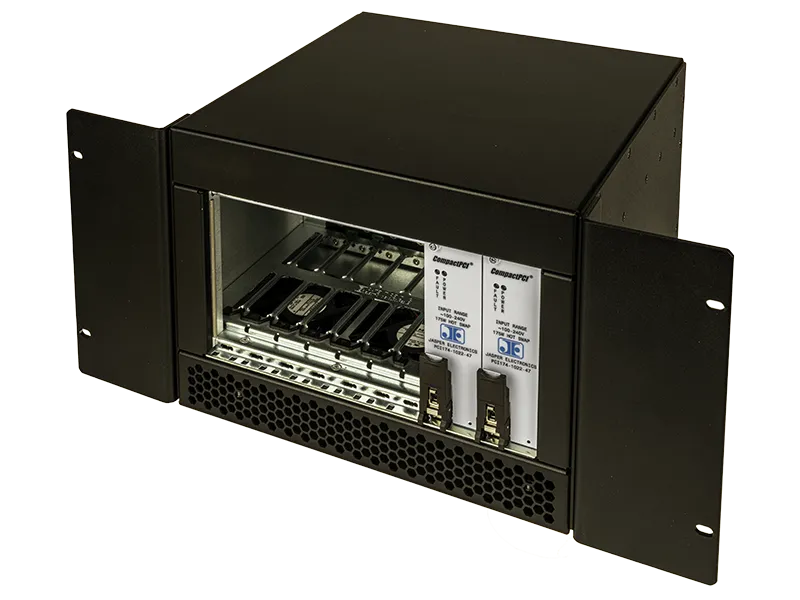

A New Approach to Producing Card Cages
Any Card, Any Pitch, Any Size, Any Bus (Standard or Custom)
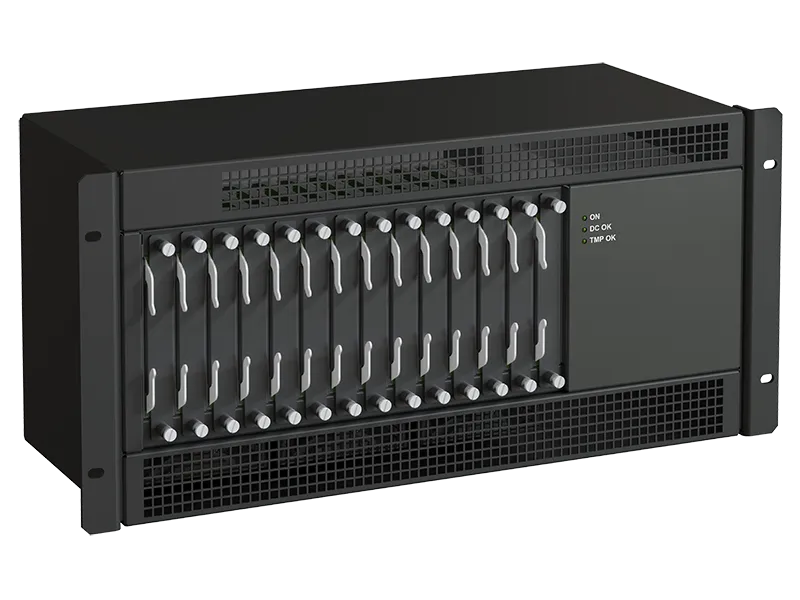
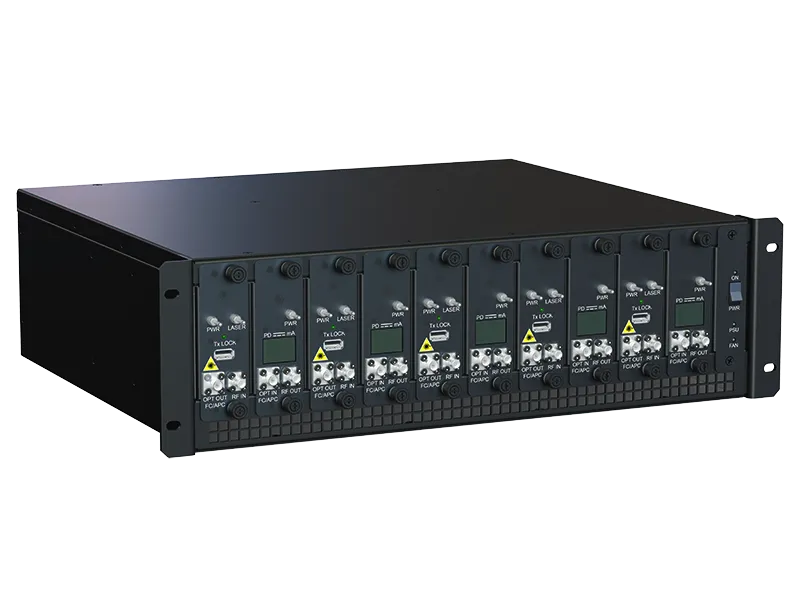
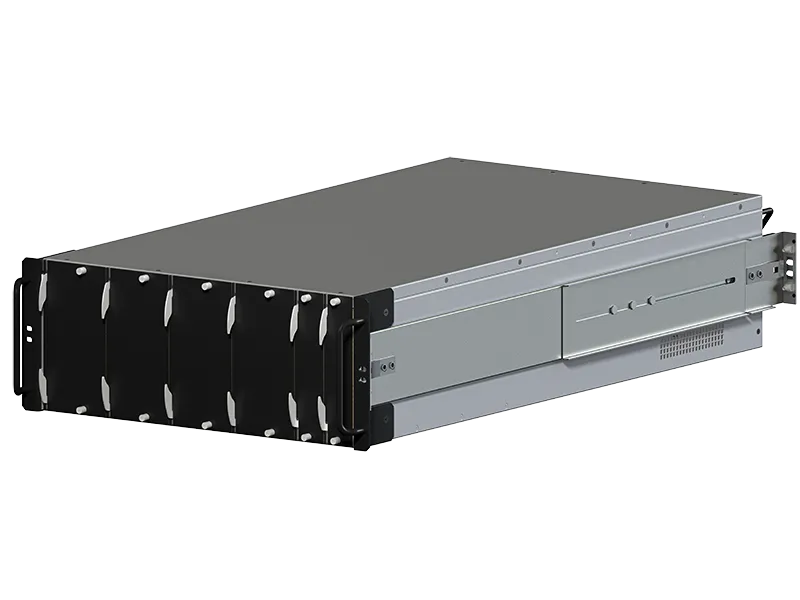
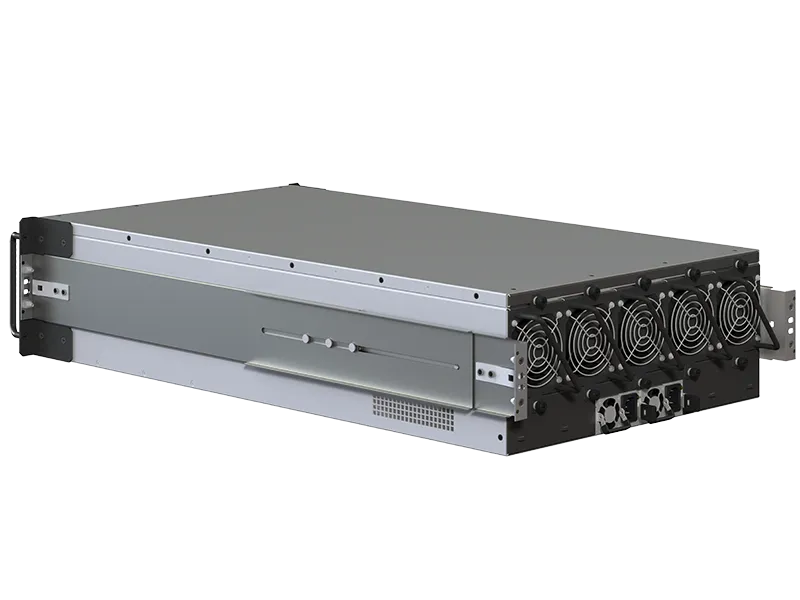
Redundant Hot-Swap Power
Single or Multiple Fans as FRUs
With fans as FRUs, a single or multi-fan tray can be replaced in fewer than 30 seconds, should a fan fail. Card cage fan trays can be made as a hot-swap FRU. We employ fans based on multiple performance criteria and coverage across the card cage.
With a vertically aligned card cage, adding fan driven active cooling generally adds 2U to the height of the card cage frame itself. Air is pulled in from the front (datacenter’s cool aisle), the fans force the cool air through the cards. The heated exhaust air exits through the top of the card cage exits out the rear (datacenter’s hot aisle). Temperature signal outputs from micros on plug-in cards can be used to control PWM fans or we can add one or more thermistors in the exit zone above the card cage to control PWM fans.
For a horizontally oriented card age, a fan tray can be on either end. This may restrict the height of your card to a standard 6U or up to ~14” (356mm) for a custom board height.
In some system where watt dissipation if quite high, like ATCA systems, multiple cooling techniques may be needed. Vapor Chambers to spread a BGA’s heat across a larger than normal heatsinks. Using dual fan trays with one pushing cool air into the card cage and a second, on the far side, pulling hot air through the card cage.
Precision and flexibility are the new keys to production rack mount card cages for any alternative board configurations, thermal considerations, and card cage requirements.