About Electronic Enclosures Inc.
Electronic Enclosures, Inc. (EEi) has a 40-plus year background in product development and brining new custom rack mount products to life for our customers. EEi was founded by Don Goss, President & CTO. Don has made a sincere practice of being available to you; new prospects, customers, and suppliers. He believes you need direct access to one who knows the finite details for accurate information to assist you in making an accurate, informed decision.
Don Goss began with years of hands-on, shop-floor experience in machining, sheet metal, and as a toolmaker, getting an education like no other. There are many misconceptions and widespread misinformation prevalent in corporate product design departments, costing companies immense profits. By knowing and understanding the traits and unique production characteristics of each model machinery and its available tooling, you will know what features in your designs are driving costs up and the alternatives. Striking a balance between product performance, regulatory compliance, quality, and costs is what this knowledge is worth. It’s rarely “one thing” that is costing you, but various design features affecting production costs and reduced profits.
Even before it became a buzz acronym, Don Goss has always practiced early supplier involvement (ESI). He has implanted ESI into our culture from the beginning. During the design process of your rack mount system, Don will tell you “If we do our design job right, we only have to do it once, but shop personnel have to make your parts over and over and over again. I want their input from the get-go”
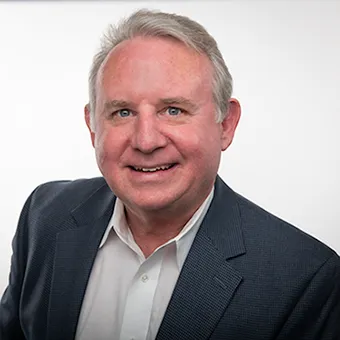